Food and Beverage Factory Engineering Service
Realization of Clients' Needs
Obayashi Group provides food and beverage factories which meet the clients' needs through custom engineering management.
By assembling a project team from our professional, well-experienced staff, and then establishing communication with the client, Obayashi Group realizes the concepts of the client. Through "custom engineering management*1", Obayashi Group realizes the clients' needs.
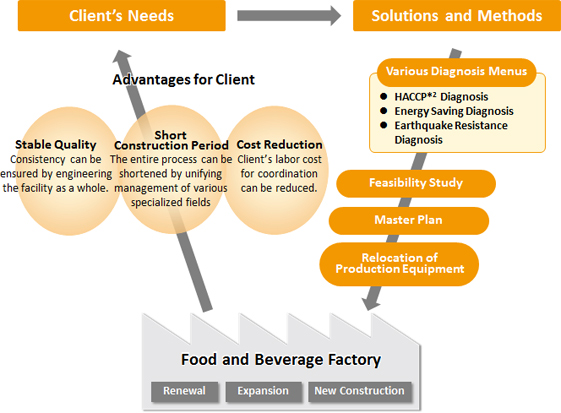
- *1 Custom Engineering Management
Our engineering technique, which places emphasis on the satisfaction of the clients, not only by offering standard technology, but also by offering technology which is best suited to clients' needs through several proposals and examinations based on clients' needs. - *2 HACCP
Hazard Analysis and Critical Control Point
Clients' Needs
Safety
- HACCP Compliance
- Safe Product Manufacture
- Stable Product Supply
Functionality
- Improved Factory Productivity
- Increased Efficiency for the Entire Factory Group
- Review of Factory Logistic
Stabilit
- A Locally Rooted Factory
- Increased Worker Motivation
- Reduced Environmental Load

Solutions and Methods
Safety
- HACCP Compliance
( Flow line planning, Zoning, Gowning planning, Insect proof, Antibacterial protection )
Functionality
- Renewal
( Review of the flow line, Work environment improvements, line restructuring ) - Review of the production base
( Factory consolidation, Factory relocation, Overseas expansion) - Optimization of factory logistics
( Automation of factory logistics, Instrumentation, MHS*3 structuring )
*3 MHS
Material Handling System
Stability
- Contribution to society ( Open factory )
- Increased worker satisfaction ( Amenity )
- Environmental protection ( Energy saving )
Meeting the various needs of food factories
Flow Line Planning, Zoning
Due to the wide variety of fresh foods produced, planning of a specific flow line for raw materials, products and people, and clear zoning for sanitary areas were designed. Furthermore, a system to prevent contamination from outside and to prevent the introduction of foreign substances was installed, achieving an environment which maintains thorough freshness and sanitary management.
Renewal
Renewal of the existing factory and the additional construction of building were carried out while the factory was under 24 hour operations. Temporary work was planned and carried out to prevent dust from entering into the existing factory. Furthermore, low-odor materials were used. Construction was planned and carried out in a way that operations of the existing factory would be affected as little as possible.
Factory Relocation
Relocation of existing factory to adjacent to existing factory at another site was planned. Multiple-layer type building, which is uncommon for food factories, was adopted to make good use of the land. Furthermore, consistency in sanitary zoning and material flow, as well as countermeasures to waterproof properties and dew condensation were taken into consideration. As a result, an industry leading factory with high-productivity was achieved.
Overseas Advance
The factory produces seasonings targeting people in overseas and is considered to be the largest base in the overseas food business. The factory contributes to increasing the company image among local customers not only by manufacturing safe products, but also by inviting visitors to view the facility.
Open Factory
The factory was highly evaluated for its HACCP compliance and high technology for cold region in a competition. The factory integrates the most advanced production line which meets HACCP and ISO14001 requirements with an enriched visitor facility to introduce the client's brand, and promote the safety and performance of its products.
Energy Saving
Engineering techniques which perceive building and production equipment as one unit were introduced. Heat emitted from the production equipment (firing room) was analyzed by air flow simulation, and a "Natural Ventilation System" which discharges the heat using natural forces was adopted in order to save energy.
Obayashi Group creates a sanitary environment for Production to keep manufacturing safe and reliable products
Realization of the factories which meet HACCP and ISO22000 requirements
Support for Clients introducing HACCP system
Promotion to establish the PRP (Pre-requisite Program) in cooperation with the clients, for stable product supply.
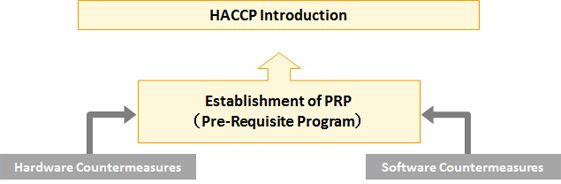
Hardware Countermeasures
Sanitary Countermeasures for the Building
- Determining contaminated and uncontaminated areas
- Flow line planning for people and goods based on contamination prevention
- Interior planning for individual rooms
(floor, wall, ceiling, door, etc.) - Environmental requirements for individual rooms
(temperature and humidity, illuminance, sanitation)
Sanitary Countermeasures for Manufacturing Machines
- Review on cleaning and anti-bacterial prevention of the equipment
(quality of material, finishing, accessories) - Design of a monitoring system corresponding to critical control points
- Prevention of cross-contamination between machines
- Securing sufficient work space
Software Countermeasures
Maintenance of the Building
- Cleaning of the Building
- Cleaning and sterilization of equipment and machinery
- Maintenance of the building, equipment, and machinery
- Environment measurement of production room
(floating bacteria, falling bacteria)
Sanitation Control for the Workers
- Management of hand washing and disinfection
- Management of clothing, footwear, etc.
- Health control for the workers
- Hygiene education for the workers
Developing a sanitation plan in compliance with HACCP, based on Abundant Experience in Food Factory Construction
Realization of a production environment with high-sanitation by establishing countermeasures to insects, rats, bacteria, and mold.
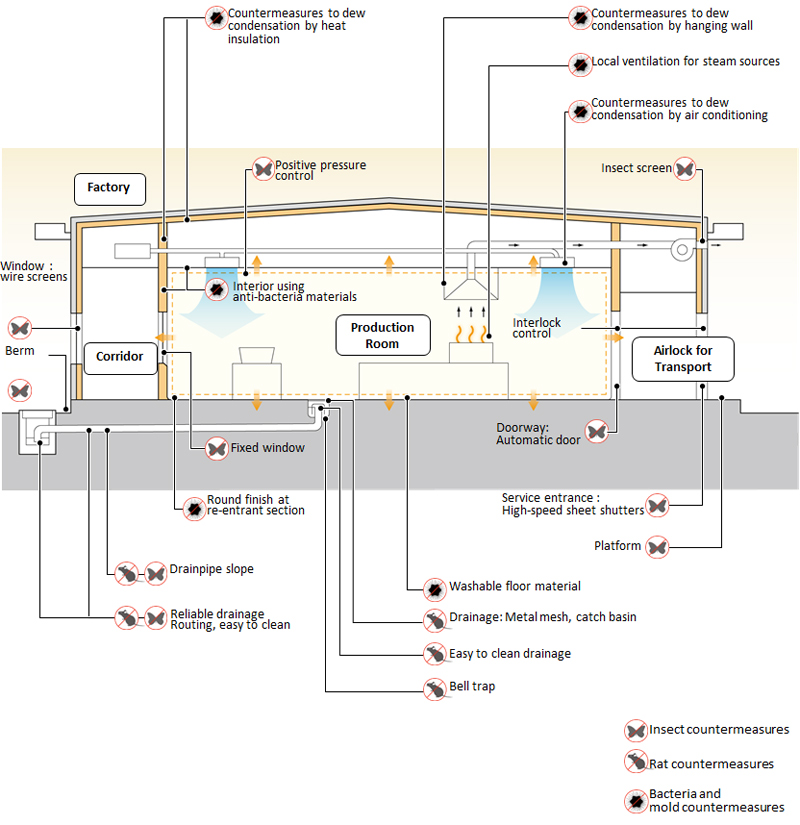
Planning the most appropriate work area and flow line in compliance with HACCP, based on the production process of each client
By zoning contaminated, semi-sanitized and sanitized areas, invasion of foreign substances will be prevented. Cross contamination will be prevented by separating people flow line from goods' one.
Flow Line of Goods and Barriers (example: Dairy Dish Factory)
Contamination by powder dust from goods and pieces of paper is prevented by barriers.
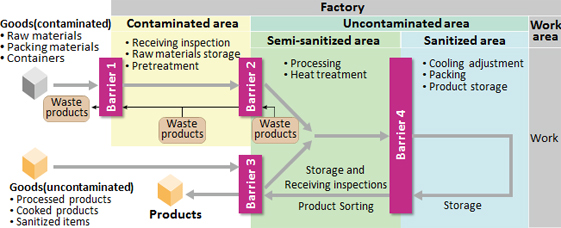
Flow Line of People and Barriers (example: Dairy Dish Factory)
Invasion of human hair, bacteria, and dust attached to clothing or shoes is prevented by barriers such as changing clothes and shoes, hand washing sterilization.
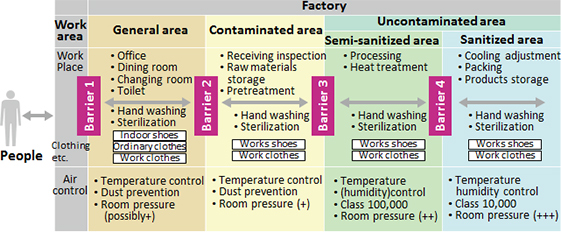
Obayashi Group has prepared an abundant technology to solve the clients' problems
Safety
Safety of the manufacturing environment is improved by emphasizing insect, rat, bacteria, and mold countermeasures based on our years of abundant experience of the food factory.
Insect and Rat Countermeasures
Countermeasures, which is reliable and friendly to environment, are established by three systematic policies and methods using minimal amounts of pesticide.
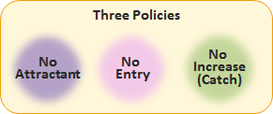
No Attractant
- Selection of wood types that insect dislike
- Insect repelling illumination
- Insect repelling window film
- Berm, pavement, and curb around the building
No Entry
- Cutout of invasion route
(Several traps, such as insect repelling trenched, etc.) - Restricted Entrance
- Double protected entrance
(Airlock, air shower) - Airtight around perimeter
(Dock shelter, sealing at interstices) - RShortened period for opening and closing
(high-speed sheet shutter)
No Increase (Catch)
- Insect catcher (for capturing, for monitoring)
Bacteria and Mold Countermeasures
Countermeasures based on the four principles for anti-bacteria and anti-mold are established in the hardware and software fields.
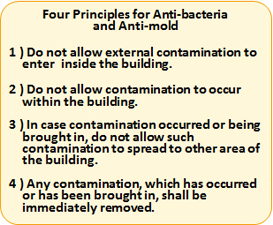
Invasion Countermeasures
- To plan the entrance preparation room
- One way toilet
Countermeasures to Prevent Occurrence or Spread
- Consideration to the floor
(Crack prevention, aridification, floor slope) - Sanitation
(Finishing, round finish of reentrant section, Stainless steel trench, Stainless steel pit) - Dew condensation prevention
(High heat insulation, ventilation to prevent stagnation, effective exhaust equipment) - Sterilization lamp
- Pressure control among areas
Elimination Countermeasures
- Sanitation (Finishing, round finish at reentrant section, Stainless steel trench, Stainless steel pit)
- RPlan of a dedicated equipment washing room
Performance
Performance can be improved through renewal aiming at better efficiency of factory, reviewing the production base, and using the most advanced systems, such as In-factory Logistics System and Manufacturing Execution Management System.
Automated Guided Transport Systems
Obayashi Group proposes specifications for the production line of the clients from our transportation technology, promoting the prevention of product contamination caused by people as well as labor-saving.
- Automated Guided Vehicle
- Automated Guided Forklift
- Automated Warehouse
- Vertical Conveyor
- Overhead Travelling Vehicle
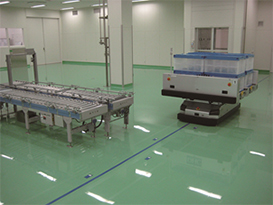
Automation/Information Systems
Providing systems which reduces worker load and errors by combining automation and information systems.
- Robotization
- Warehouse control system
- Sorting and load alignment system
- MES (Manufacturing Execution System)
- In-factory traceability establishment
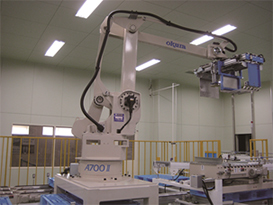
Stability
By viewing the stakeholders (investors, customers, local community, business partners, employees, future generations, etc.) from the viewpoint of CSR (Corporate Social Responsibility), a factory aiming at synergetic growth between company and society will be achieved.
Persistent Management
Regarding various risks, several techniques are presented to promote stable production in the factory.
- BCP (Business Continuity Plan) Support
- Seismic diagnosis, Seismic reinforcement
- Renewal for HACCP compliance
- Food defense (security) countermeasures
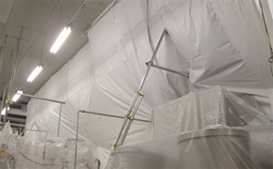
Contributing to Society and Employee Satisfaction
Offering open factory to contribute to society, and amenity spaces for employees' comfort and liveliness.
Contribution to society
- Visitor's corner
- Experience corner
- Direct sales corner
Employee satisfaction
- Open dining hall, rest area
- Sleep break, shower booth
- Employee interaction area
Consideration for the Environment
Obayashi Group offers best combination of energy saving methods for factory of the client through simulations.
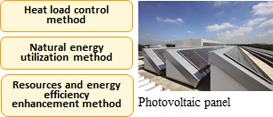
Energy saving simulation software "Eco-Navi*4"
*4 Eco-Navi
Comprehensive evaluation system for energy saving buildings developed by Obayashi Group
This simulation software estimates building LCCO2 and reduction effect of energy cost by seeking the best combination of energy-saving methods suited to the client's budget.
*1 Atrium room temperature adjustment
*2 Blocking external air
*3 Total heat exchanger
*4 Airflow window
*5 Reduction of duct resistance, large temperature difference in water
*6 Cogeneration + water heat storage, highly efficient lighting, etc.
*7 Draft prevention, Exterior wall insulation
*8 VAV-VWV
*9 Ventilation power reduction
*10 Outdoor air cooling,CO2 control
*11 Solar power generation, Green roof
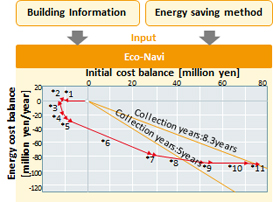
Various Diagnostic Menus to Support from Planning to Operation of Manufacturing Environment
Obayashi Group supports plans for renewal, extension and new construction by diagnosing the existing manufacturing environment and "visualizing" the effects of the planned techniques to be introduced by simulation.
Microbe Measurement
Diagnostic menu by our technical research institute to perform gene analysis and to make a report for floating bacteria and falling bacteria collected in work area.
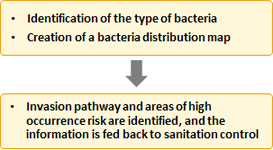
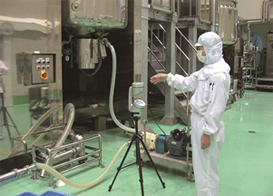
Airflow Analysis
This simulation "visualizes" airflow in the work area in motion at each time.
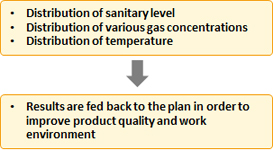
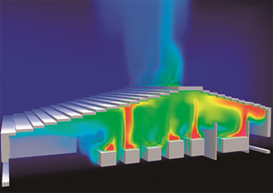
Major Project
-
Oisis Shiga Factory
Shiga, Japan -
TAIKO SUISAN Freezing Seafood Processing Plant
Miyagi, Japan -
AJINOMOTO Ayutthaya Factory
Ayutthaya, Thailand -
Nippon Flour Mills Kobe-Konan Mill
Hyogo, Japan -
SONTON FOOD INDUSTRY New Osaka factory
Osaka, Japan -
NISSHIN FOODS VIETNAM New Factory
Binh Duong, Vietnam -
NIHON CANPACK Tonegawa Factory
Gunma, Japan -
SUNTORY Beech Forest Factory
Tottori, Japan -
NISHI-NIHON MYOJO Kobe Factory
Hyogo, Japan -
Mercian Nikko Plant
Tochigi, Japan -
Nippon Flour Mills Chiba Mill
Chiba, Japan -
AJINOMOTO Nong Khae Factory
Thailand -
ASAHI BREWERIES Kanagawa Factory
Kanagawa, Japan -
SUNTORY Takasago Plant
Hyogo, Japan -
S&B Foods Miyagi Plant
Miyagi, Japan -
Kirin Brewery Kobe Factory
Hyogo, Japan -
Tatsuuma-Honke Brewing Sake Brewery
Hyogo, Japan -
Hakushika Sake Brewery
Colorado, U.S.A.